When deciding on a surface treatment for your aluminum profiles, you usually have several options. Each method, whether anodizing, powder coating, or painting, has advantages and disadvantages.
What is powder coating?
In this article, we will discuss powder coating aluminum extrusion profiles. Architectural aluminum profile powder coating technology has advanced rapidly in recent years. It is distinguished by the absence of a solvent and the absence of environmental pollution. Furthermore, the powder is recoverable, simple to use, and the coating color is diverse, allowing it to meet the requirements of different weather resistance. Most factories are now automating the production process for powder coating aluminum profiles.
History & Application
Powder coating has been widely noticed by the entire world since its introduction in the early 1970s because it does not contain toxic gas. All of the powder can be made into coatings. Furthermore, the processing of powder coating aluminum profiles is high efficiency, with good protection and decorative overall performance, among other benefits. As a result, it is widely used.
Aluminum profile powder spraying is classified as outdoor powder spraying, indoor powder spraying, anticorrosive powder coating, and so on. It is widely used in aluminum frames, balconies, corridors, doors and windows, and other places.
What factors influence the weight of aluminum profiles in powder coating?
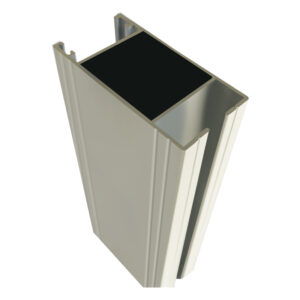
-
1, Flowability of powder
Under the same external conditions (such as production technology, aluminum profile geometry, and so on). The powder coating rate is the most important factor influencing the entire spraying area. The electric field force of powder particles is the main adsorption force of electrostatic powder spraying, according to the principle of electrostatic powder spraying.
The powder rate on the surface of an aluminum profile is determined primarily by the number of powder particles. Coulomb’s law states that the charge of powder coating particles has the following relationship over time:
Qs= 3πε0 (ε-1)/(ε+2)d²E
Qs ——The charge of the powder particle
ε ——Dielectric constant of powder
D —— radius of powder particle
E ——electric field strength
To improve the powder rate of the aluminum surface, we must increase the charged capacity of the powder particles. When the powder rate is increased, the total area of spraying is increased correspondingly under the same conditions as before.
-
2, Composition of powder
The base stock in the formulation has the greatest influence on the dielectric constant in powder coating composition. All aluminum factories, in general, use polyester resin for outdoor aluminum profiles, outdoor aluminum handrails, and aluminum window frames. As a result, the powder content has the greatest influence on the permittivity of powder coating. In general, the more basic the stocks, the easier they are to absorb by static.
The base stock in the formulation has the greatest influence on the dielectric constant in powder coating composition. All aluminum factories, in general, use polyester resin for outdoor aluminum profiles, outdoor aluminum handrails, and aluminum window frames. As a result, the powder content has the greatest influence on the permittivity of powder coating. Typically, the more basic the stocks, the easier they are to absorb by static.
Second, the dielectric constant is related to the powder’s water absorption. The powder loading rate is reduced when the powder is slightly moist.
Furthermore, the radius of the powder has a significant impact on the powder loading rate. Because of the small particle size, ultrafine powder (radius < 10m) requires less electricity and is easily removed by the exhaust fan.
If the powder is too thick, gravity prevents it from easily adhering to the surface of the aluminum profile, and it slides down quickly. Aluminum profile manufacturers should purchase powder within D50 when purchasing powder based on coating thickness requirements.
-
3, Different colors and types of powders
If the film thickness of aluminum profile spraying is thicker, it requires more powder to spray the same area in the normal spraying process. The thickness of the sand powder coating was found to be between 50 and 70μm during an inspection of the coating at the Cheetah Aluminum plant. The film thickness of ordinary powder is approximately 70-90μm. As a result, ordinary powder is sprayed less than sand grain powder.
In the domestic market, it is common to use grey sand grain powder coating on aluminum window frames, and white powder coating on export profiles. We must not only keep the color of the aluminum surface consistent, but also make it smooth and flat.
-
4, Quantities of the order of powder coating aluminum
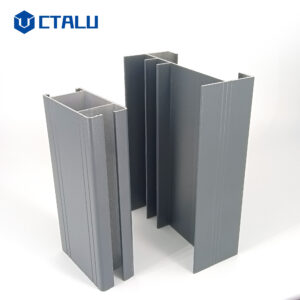
Because there is waste when spraying, the machine needs to be cleaned and the powder changed frequently when there are few individual colors in the spraying order. It will increase waste and loss, resulting in a smaller final calculation for our factory’s factory per kilogram of spray area.
We can infer from the foregoing that while small orders result in more waste, large orders not only result in less waste but also increase the capacity of aluminum profiles. This is the reason we’ve always required a MOQ of at least 2-3 tons for each color.
-
5, Geometry of aluminum extrusion profiles
Overall, aluminum extrusion plants calculate the total area per kilogram of powder spray. In fact, the total area of each profile is divided into decorative (also known as production) and non-decorative areas.
During the spraying process, the film sprayed on the decorative surface will be thicker than the film sprayed on the non-decorative surface. As a result, the decorative surface of the same area requires more powder coating than the non-decorative surface, and because the decorative area of the aluminum profile accounts for a larger proportion of the total area, more powder is consumed. In other words, the smaller the total area of powder spraying per kilogram.
Cheetah Aluminum has a complete aluminum profile production line, from mill finishing, to any kind of surface treatments, such as anodizing profiles or powder coating profiles, wood grain or electrophoresis.
Any questions please send to us, please feel free to contact:
Email: simon@ctalu.com